■ Ruido aerodinámico y vibraciones
En gases y vapor de agua, un derrame crítico por alta presión diferencial se manifiesta en forma de ruido. El coeficiente asociado es xT –Pressure drop ratio factor, especifico de cada válvula, siendo “Pressure drop ratio” x = ∆p / P1 .
El ruido se atenúa con válvulas de diseños especiales del trim que reducen la velocidad y buscan más altas frecuencias no audibles. Son las válvulas multihole y otras combinaciones multi-stage / multi-path. Cada fabricante ofrece varios tipos eligiéndose el que se requiera en cada aplicación.
Un problema patológico en estos diseños es su mal comportamiento cuando el fluido tiene partículas ya que por los pasos estrechos y la forma laberíntica de su construcción, tienden a obstruirse produciendo también desgastes y agarrotamientos sobre todo, en los trims guiados por jaula.
Todo ruido lleva asociado un nivel de vibraciones que además de afectar a la válvula se transmiten por la tubería a equipos adyacentes. Se están analizando con más detalle la influencia de las vibraciones sobre todo en válvulas para servicios severos, pues producen fatiga de materiales del trim. Por tanto, el ruido no es sólo un problema por si mismo; obliga a buscar el diseño adecuado que permita paso de partículas y además hay que poner más atención en el punto de instalación de la válvula en la tubería y el diseño de piping.
■ Fugas internas. Pérdida de estanqueidad.
Esta es una de las características técnicas de las válvulas que más cuesta mantener. La perdida de calidad de cierre depende de los desgastes que se produzcan por alguna de las causas que se han visto anteriormente. Lo importante es que el aumento de fuga no produzca una degradación de los internos y vaya en aumento.
Las válvulas de control se fabrican con una determinada fuga, previamente especificada, respecto a unas normas ANSI/FCI 70.2 /IEC 534-4, que son las dos más usadas. Las fugas en el proceso serán distintas, con el fluido real a la presión y temperatura de trabajo. Lo que se especifica y se compra es una determinada “calidad constructiva de cierre” para unas condiciones de prueba. (Para más detalle ver articulo publicado en este blog de ISA : FUGAS EN V. DE CONTROL; 1ª Parte, 27 Junio 2018) [isaespana.wordpress.com]
La fuga también puede depender del actuador, del posicionador, defectos de alineación y centrado del trim por mal montaje durante operaciones de mantenimiento, presencia de partículas, etc.
Los cierres tienen diferente configuración según sea el tipo de válvula: globo simple asiento, equilibradas guiadas por jaula: sin o con piloto, rotativas, mariposas, etc. Siendo el trim el corazón de la válvula, sus materiales y calidad de mecanizado, así como la buena selección del actuador, son los puntos más importantes a cuidar. Una válvula no cierra mejor aumentando la presión de aire (cuando sea “aire cierra”). Esto puede provocar un exceso de asentamiento que deteriore el trim o doble el vástago. Tan malo es un actuador insuficiente como otro excesivamente sobredimensionado.
La detección de fugas peligrosas en el trim, que pasen de un valor, no es un asunto sencillo. Podría detectarse pero no cuantificarse. En este sentido se han intentado procedimientos mediante ultrasonidos y termografía, pero cada fluido, industria y entorno de proceso son diferentes, requiriendo unos análisis comparativos que normalmente no dan resultados satisfactorios.
■ Fugas al exterior
Los puntos típicos de fugas al exterior son la unión tapa-cuerpo en todas las válvulas de globo y en la zona del vástago por la estopada, en válvulas alternativas como en las rotativas: mariposa, bola, macho, etc.
El mantenimiento de la estanquidad en la empaquetadura, depende que haya sido bien seleccionada y montada, también de la frecuencia de maniobras y de su apriete. Ahora, para minimizar intervenciones, se añaden resortes de apriete controlado y constante en los tornillos apriete de estopada. También hay diseños que incorporan juntas tóricas que refuerzan a la estopada, siempre que sean compatibles con la naturaleza del fluido. Hay que indicar el mejor comportamiento de las válvulas rotativas por su menor fricción y mayor capacidad de cierre en las estopadas.
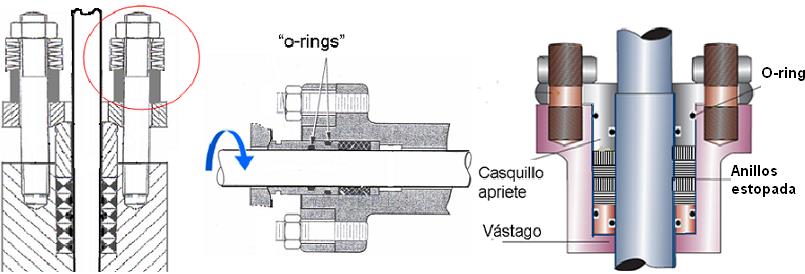
Las fugas entre tapa-cuerpo normalmente se deben a un deterioro de la junta usada así como del diseño mecánico de la unión tapa-cuerpo, que pueden ser varios. También se producen fugas por defecto de alineación en el montaje o deficiente apriete de los tornillos de cierre de la tapa-cuerpo. Esta tortillería debe ser del material adecuado y apretados con el par que recomiende el fabricante mediante llave dinamométrica. Se dispone ahora de equipos hidráulicos que aportan pares de apriete controlados y uniformes en todo el perímetro.
(Con más detalles ver articulo publicado en este Blog de ISA: FUGAS EN V. DE CONTRO, 2ª Parte 29 Junio 2018)
Actualmente hay la posibilidad de detectar las fugas y transmitir esta información mediante técnica wireless, si la severidad de la aplicación lo justifica, por ejemplo en fluidos peligrosos.
Agresiones externa en la planta
Los equipos de un lazo de control que van instalados en el propio proceso son básicamente dos: los medidores y transmisores de la variable a controlar (caudal, presión, nivel, temperatura, etc.) y el elemento final que, en nuestro caso es la válvula de control. Estos transmisores, aunque instalados en las tuberías ó sobre los equipos, no producen perdida de presión en el fluido, por lo que no suelen sufrir desgastes internos, salvo corrosión. Sólo hay que considerar el ataque externo de un medio ambiente agresivo por vapores, fugas, inclemencias atmosféricas que son fácilmente solucionables mediante elementos de protección: bolsas, cubiertas de plástico, armarios de inoxidable, etc.
Muchas válvulas de control están situadas a cubierto pero otras muchas no. Es por esto que la válvula sufre todos los efectos del medio ambiente, tanto las condiciones atmosféricas, moderadas o extremas, como la combinación de estas condiciones climáticas asociadas a gases y polvos que pueden producir un ataque corrosivo sobre, cuerpo, actuador, posicionador, accesorios y tuberías neumáticas de señal.
Algunos procesos químicos industriales son especialmente agresivos como fertilizantes, siderurgia, papel, etc. También en países con climas extremos por altas o bajas temperaturas, tormentas de arena en zonas desérticas, oleoductos y gaseoductos, torres de explotación off-shore ó plantas próximas al mar, etc.
Cada aplicación particular, se debe analizar previamente, en fase proyecto, buscando experiencias de situaciones similares; se adoptarán medidas constructivas en cuanto a materiales de cuerpo y actuador así como elementos de protección para que la válvula y sus accesorios resistan esas situaciones y mantenga sus prestaciones de control con una alta disponibilidad.
Se cuidará el procedimiento y tipo de pintura más adecuado a cada caso, así como las juntas de cierre y sellado, sobre todo en los accesorios, como el posicionador, electroválvulas, etc. En situaciones límite se deberá proteger, sobre todo el conjunto actuador y accesorios, con forros, bolsas o armarios metálicos específicamente diseñados para cada válvula. Hay empresas dedicadas a solucionar estas situaciones.
3 – Otras causas
■ Fallos de especificación durante la ingeniería. Errores de cálculo y selección.
Cada vez son mejores los programas de cálculo para definir el tamaño del trim de las válvulas de control. Sin embargo se constatan muchas deficiencias en el proceso de selección.
El éxito de una válvula, en el contexto de un lazo de control, depende de:
– Haber definido bien sus condiciones de operación: regímenes de caudal, presiones, variaciones de carga, etc.
– Que se haya hecho una buena selección del tipo y tamaño, del trim para esa aplicación en concreto.
– Que se hayan elegido los materiales adecuados que componen el trim
“El coste de una válvula de control no es su precio de compra, si no: precio de compra + puesta en marcha + mantenimiento en los primeros 5 años”
Los problemas más frecuentes surgen del sobredimensionamiento, o cuando se aplican criterios generales sin haberse preguntado en concreto y con rigor, por ejemplo: ¿Qué se espera de esta válvula? ;¿Cómo se la va a operar? ; ¿Cuáles van a ser las variaciones del proceso?; ¿Cuántas veces tiene que cerrar?, ¿Con que estanqueidad debe hacerlo ?, etc.
Otros problemas proceden de hacer por separado la selección de la válvula sin conocer ni tener en cuenta el diseño de las tuberías . Según sea el fluido y las condiciones del derrame, ambas cosas pueden afectar al diseño del piping y a la ubicación de la válvula en un lugar más idóneo.
“El mantenimiento empieza en el proyecto”.
Esta frase es conocida pero generalmente olvidada durante el desarrollo de la ingeniería el montaje y la puesta en marcha.
■ Problemas derivados del montaje y diseño de tuberías, y de la puesta en marcha.
La válvula de control se instalará en aquel punto del proceso donde se obtenga el mejor control y más rápida respuesta sobre la variable controlada, según sea el fluido.
El diseño de las tuberias puede afectar a la válvula. Esto ocurrirá, sobre todo, en derrames críticos, tanto con líquidos como con gases o vapor. Se evitarán diseños de líneas y codos que produzca fuertes turbulencias ó vibraciones que puedan afectar a la estabilidad, bien de los órganos internos de las válvulas ó a sus instrumentos asociados, sobre todo el posicionador digital.
En el caso de líquidos, se procurará dejar un tramo de tubería, aguas arriba pero, sobre todo, aguas abajo. Habrá procesos y fluidos que requieran unas distancias mínimas, sobre todo en cuanto a alejar los codos aguas abajo. Un codo próximo a la salida es perjudicial en un régimen de cavitación pero mucho más cuando hay flash o partículas abrasivas. Por eso las válvulas con posibilidad de vaporización se colocarán lo más cerca posible del depósito ó recipiente de descarga.
Desde el punto de vista del montaje, lo mejor es que las tuberías sean horizontales ó ligeramente inclinadas. Pueden montarse las válvulas en tuberías verticales, según diseños, y tamaños, pero siguiendo recomendaciones de cada fabricante; esta posición paralela al suelo, aunque no impide su trabajo, si puede ser un inconveniente posterior para el mantenimiento, sobre todo si la válvula es grande o va soldada a la tubería.
■ Mantenimiento inadecuado en las primeras intervenciones.
Una válvula de control debe durar muchos años y como instrumento requerirá verificaciones y mantenimiento en cuerpo, actuador y accesorios localmente. Por tanto la accesibilidad para un mínimo tiempo de reparación debe ser un objetivo. Por tanto se estudiará el acceso para su maniobra, montaje y desmontaje con el mínimo de elementos auxiliares: plataformas, polipastos, etc. pensando en poder acceder a los internos de la válvula: obturador-asiento y actuador de la forma más fácil posible.
“Cada diseño de válvula tiene su mantenimiento especifico”.
“En los servicios severos se precisa personal con experiencia y conocimiento del equipo a intervenir”
No se han mencionado en este articulo los problemas y averías en actuador y accesorios. Por su naturaleza entran ya en el terreno propio de la instrumentación. Se ha mencionado que las condiciones ambientales pueden afectar al actuador como equipo mecánico; también tienen sus averías propias según sea de diafragma, de pistón ó eléctricos. Los accesorios y fundamentalmente aquellos que están en la línea de transmisión de la señal de control, son particularmente sensibles y deben ser adecuadamente protegidos frente al medio ambiente y por altas ó bajas temperaturas: posicionador electroneumático, transmisores de posición, electroválvulas, relés de bloqueo, etc.
Antonio Campo López
Profesor-coordinador en el Master ISA/Repsol de Instrumentación y Control.
Autor del libro: VALVULAS DE CONTROL Selección y Cálculo. ( Díaz &Santos)
Edición Revisada 2018
CONTENIDO
1.- La válvula en el lazo de control; parámetros que definen su respuesta dinámica.
2.- Tipos y selección de válvulas de control.
3.- Los actuadores, posicionadores y demás accesorios.
4.- La válvula como instrumento; ganancias real e instalada. Posicionadores digitales y su integración en los sistemas de control y gestión.
5 y 6.- Análisis de derrames en líquidos y gases; coeficientes asociados para el cálculo.
7.- Aspectos mecánicos: materiales, estanqueidad, fugas, etc.
8.- Fórmulas de cálculo y procedimientos.
9.- Cálculos; ejemplos; consejos prácticos generales.
-
Editorial: Díaz de Santos (Colección ISA-España)
-
ISBN: 978-84-9969-799-4- Casa del Libro: http://www.casadellibro.com – Amazon: http://www.amazon.es y otras librerias especializadas.
-
Diaz de Santos: http://www.editdiazdesantos.com/libros/campo-lopez-antonio-valvulas-de-control-seleccion-y-calculo-L27007990101.html